Lean Six Sigma Green Belt Certification
Course Description
Take your Lean Six Sigma knowledge to the next level
Self-paced and fully supported, our online and tutored LSS Green Belt programs create the capacity for change in your organization. The Juran method ensures everything you learn is fully understood and tested in your business environment. By the end of our program, you will have the skills to identify and begin solving the challenges faced by your business.
Our 2024 program begins in August, and November. You can select one of these options from the Start Date menu below.
Green Belt with Statistics
This program is most suitable for manufacturing settings. You can use the data analysis skills and knowledge you acquire directly to evaluate the more complex kinds of technical and production processes your business may have.
- 26.42 hours of self-paced learning
- 6.5 hours of live webinars with a certified Juran instructor
- 3.29 CEUs
- Price: Price: $850 (Training) / $2,850 (Training & Certification)
Green Belt for Healthcare, Government and Services
This program is most suitable for service organizations such as those in healthcare, hospitality, and government. You will learn how to improve processes in a more service-orientated business, with a focus on customer experience.
- 19.75 hours of self paced learning
- 4.5 hours of live webinars with a certified Juran instructor
- 2.43 CEUs
- Price: Price: $850 (Training) / $2,850 (Training & Certification)
*Minitab is highly recommended for Green Belt with Statistics. To purchase Minitab, please go to Minitab.com
*The certification package includes everything you need to become a Certified Juran Green Belt! This includes 8 hours of personalized project coaching, exam, and oral project review.
On-Demand Now Available
Worried about missing a live webinar? Join our on-demand program for recorded live sessions, and a little bit of a discount! Simply select “On-Demand” in the Start Date box above!
Group Training
Interested in this program for a team? We offer online, blended, and onsite training for Lean Six Sigma Green Belt. Fill out the form below to hear about how we can create a customized learning experience for your organization!
Contact us for more details!What is involved in the Lean Six Sigma Green Belt course?
Our Green Belt course is designed and delivered by Juran certified coaches with an extensive knowledge of Lean Six Sigma tools and methods.
- Objectives
- Project Work
- Training
- Belt Certification
- Completing a Lean Six Sigma DMAIC improvement project.
- Learning the Lean and DMAIC methods for improvement.
- Learning both graphical and primary statistical tools that enable the Lean and DMAIC methods.
- Applying methods and tools to real quality and performance problems.
- Practicing team leadership skills.
Participants will have to successfully complete a Lean Six Sigma DMAIC improvement project to attain LSS Green Belt. A Juran certified coach will help you identify a suitable project within your organization, and equip you with the skills and knowledge to deliver it.
You can start learning at your own pace online, with access to all the materials and insights you need to achieve structured learning outcomes. As you progress, live webinars complement the program giving you a chance to interact with course leaders and fellow students. The collaboration is an invaluable part of the learning experience.
Participants have the option of taking the course with or without certification. Those who opt for certification will receive a Green Belt certificate upon completion of:
- One improvement project, as approved by Juran instructor
- Online exam (score of 70% required to pass)
- Eight hours of project coaching
- A two-hour oral project review with a Juran Certifier
- Final project storyboard report
LSS Green Belt Course Topics
- Green Belt Without Statistics
- Green Belt With Statistics
- The history of quality and continuous improvement
- Basic quality
- The Juran management system
- The Juran Trilogy
- The need for change and continuous improvement
- How to improve quality
- Introduction to variation and waste
- Continuous improvement structures
- Effective team membership
- Overviews of improvement methods (DMAIC, Lean, Root Cause Corrective Action, Quality by Design)
- Introduction to Selecting Projects
- Identifying the Costs of Poor Quality
- The financial case for improvement
- Introduction to the Cost of Poor Quality
- Design
- Measure
- Analyze
- Improve
- Control
- Stakeholder analysis
- Voice of the Customer Matrix
- SIPOC Diagram (High-Level Process Mapping)
- Calculating Sigma Level and Process Yield
- Pareto Analysis
- Data Collection Plan
- Sampling
- Detailed Process Mapping
- Graphs and Charge
- Brainstorming
- Stratification
- Histograms
- Box Plots
- Scatter Diagrams
- Cause-Effect Diagrams
- 5-Why Analysis
- Failure Mode and Effect Analysis
- Impact Control Matrix
- 6S
- Value Stream Mapping
- Spaghetti Diagrams
- Demand and Capacity
- Solution Matrix
- Barriers and Aids Chart
- Pilot Study
- Mistake Proofing
- Benchmarking
- Pugh Matrix
- Process Control Plan
- Control Charts
- The history of quality and continuous improvement
- Basic quality
- The Juran management system
- The Juran Trilogy
- The need for change and continuous improvement
- How to improve quality
- Introduction to variation and waste
- Continuous improvement structures
- Effective team membership
- Overviews of improvement methods (DMAIC, Lean, Root Cause Corrective Action, Quality by Design)
- Introduction to Selecting Projects
- The financial case for improvement
- Introduction to the Cost of Poor Quality
- Design
- Measure
- Analyze
- Improve
- Control
- Stakeholder analysis
- Voice of the Customer Matrix
- SIPOC Diagram (High-Level Process Mapping)
- Measurement System Analysis
- Process Capability
- Calculating Sigma Level and Process Yield
- Pareto Analysis
- Data Collection Plan
- Sampling
- Detailed Process Mapping
- Graphs and Charge
- Brainstorming
- Stratification
- Histograms
- Box Plots
- Scatter Diagrams
- Cause-Effect Diagrams
- 5-Why Analysis
- Failure Mode and Effect Analysis
- Impact Control Matrix
- 6S
- Value Stream Mapping
- Spaghetti Diagrams
- Demand and Capacity
- Introduction to Hypothesis Testing
- One Proportion Tests
- Two Proportion Tests
- Chi-Square Test
- Normality Tests
- Test for Equal variance
- 1 Sample t-Test
- 2 Sample t-Test
- Analysis of Variance
- Nonparametric Tests for Green Belts
- Correlation and Regression for Green Belts
- Solution Matrix
- Barriers and Aids Chart
- Pilot Study
- Mistake Proofing
- Benchmarking
- Pugh Matrix
- Introduction to Design of Experiments
- Process Control Plan
- Control Charts
- Control Charts in Minitab
- Statistical Process Control
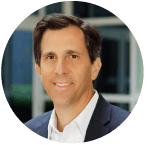
Admissions Process
Green Belt FAQs
Here are the answers to some of the most frequently asked questions about our Lean Six Sigma Green Belt training course.
As an LSS Green Belt, you will have the opportunity to deliver small-scale improvement projects which, if successful, can bring a genuine sense of fulfillment. Indeed, there aren’t many things as empowering as knowing that you’ve had a genuine impact on the productivity and financial performance of your company.
Professionals with LSS Green Belt certification will usually spend between 25% and 50% of their working hours on Lean Six Sigma projects. They are generally considered to be experts in Lean Six Sigma methodology and a driving force for quality in their organization.
No they do not. However, a candidate should fit a belt-specific profile and meet the explicit nomination criteria for that belt. They should also possess the knowledge, skills and experience that are required to be successful at the specific belt. Generally, candidates can start with Yellow, Green or Black Belt training, and can discontinue training at any belt level.
Lean is the process of optimizing organizational systems by eliminating or at least reducing, the “waste” within them. Six Sigma is a quality improvement method that seeks to improve process effectiveness. The integration of Lean and Six Sigma has become known as Lean Six Sigma, delivering both improved efficiency and effectiveness.
Minitab is not a hard requirement for our programs. However, for Green Belt with Stats, Black Belt, and Upgrade to Black Belt, it is highly recommended. The instructor will reference and showcase many statistical tools and concepts using Minitab and therefore it will make your certification journey much easier in comparison to using Microsoft Excel.
According to Salary.com, the average salary in the United States for somebody with Lean Six Sigma Green Belt certification is $104,300. The range typically falls between $84,700 and $110,200, and can be affected by a number of factors including additional skills and certifications, education, the number of years somebody has worked in their chosen profession, and the industry in which they operate.
We usually prefer that you pay for Green Belt training with a credit card. However, if you would like to be invoiced, please reach out to mstamp@juran.com. We also allow for flexible payment schedules, when required.
Green Belts typically have less of a leadership role than Black Belts, hence why the latter tend to demand a higher salary than the former. In general, project teams will comprise a number of Green and Yellow Belt professionals who will be responsible for actioning improvements under the guidance of a certified Black Belt.
A Green Belt’s understanding of Lean Six Sigma methodologies won’t be as advanced, but they will still possess the necessary knowledge to solve quality problems and perform analysis using the relevant tools. Black Belts, on the other hand, will have a thorough understanding of Lean Six Sigma and an ability to lead successful improvement projects.